What to do About the Battery Talent Shortage?
Is there a battery talent shortage, and if so, what can we do about it?
Thank you for reading Lithium Horizons. Here we explore energy, innovation, and ideas from the frontiers of materials. You can subscribe for free to receive new posts directly in your inbox.
As demand for batteries surges, the battery industry is facing a critical shortage of skilled workers. A report from the Center for Automotive Research paints a grim picture of the workforce challenges ahead. The organization surveyed 158 North American professionals in the electric vehicle (EV) and battery industries and found that 82% reported shortages of skilled local applicants. Globally, Billy Wu, an associate professor at Imperial College London, estimates that between 300,000 and 1,400,000 battery jobs may need to be filled by 2030. This represents a significant number of individuals who require training in areas such as electrochemistry, battery materials, battery management systems, product and system design, manufacturing, and safety.12
My personal experience confirms this trend. Each time I hired, it was an uphill battle to find suitable candidates locally. Although frustrating, we should not be surprised; battery technology is complex!3
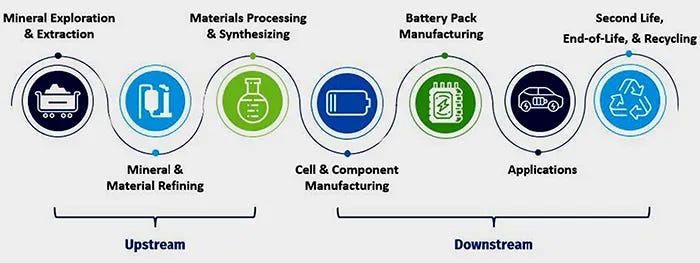
Advancements in battery technology result from the collaboration of multiple disciplines (Figure 1). Materials scientists develop new materials and integrate them into innovative cell designs. Industrial engineers optimize manufacturing methods for mass-producing these cells. Electrical engineers wire the cells together and design state estimation algorithms. Mechanical engineers design battery modules and packs with appropriate structural and thermal properties. As you can see, a wide spectrum of expertise is required, and no single course or college major can make someone an expert in all aspects of battery technology. It is unrealistic to expect one individual to possess all the necessary knowledge, from the nanoscale to the macroscale, from raw materials to recycling (Figure 2).
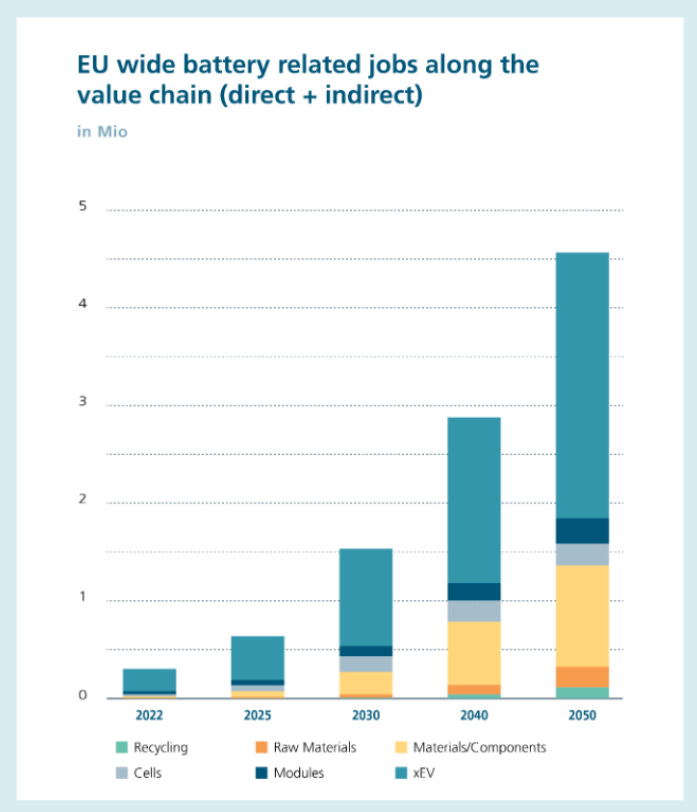
What often happens is that individuals from diverse backgrounds focus on their specific areas of expertise, frequently overlooking how their work relates to other segments of the battery value chain. A common example is the development of high-energy-density batteries without considering how these batteries can be mass-produced. It may turn out that their production is prohibitively expensive, preventing these batteries from ever seeing the light of day (these are the batteries you read about in popular science magazines every few months). Successful battery development projects depend on understanding these interconnections from the very beginning.
This brings me to a set of practical steps that can be taken to address the battery talent shortage:
Advanced degrees in battery research and development should not overlook the development part. These programs should emphasize how research can be applied to real-world scenarios. Students should be offered courses that introduce economics, manufacturing, and logistics related to battery mass production. Collaboration with industry players through internships is highly promising, as it prepares students for the realities of the battery industry.
Traditional engineering degrees, such as mechanical and electrical engineering, should incorporate courses on battery science, teaching the basics of electrochemistry and battery materials while focusing on the role of these degrees in the battery industry. Likewise, battery-specific degrees should include courses on the mechanical and electrical engineering aspects of batteries, in addition to the usual focus on materials and electrochemistry.
Upskilling through professional training programs in battery engineering is essential. A good example is Battery Associate’s BatteryMBA, a course that combines technical and business knowledge for the battery industry and is suitable for workers transitioning from adjacent non-battery industries. Another example is the InnoEnergy Skills Institute. Standardizing core tenets of battery knowledge would help ensure high-quality training for battery professionals. The Battery Workforce Initative, for instance, develops consensus on core training needs and creates training programs for use by companies and local training providers.
In summary, greater coordination between employers and educators is essential. Upon closer examination, it becomes clear that battery talent is available; there is no shortage. Thousands of new employees with good technical foundations enter the job market each year who are capable of working in the battery industry. They simply need to be provided with the proper tools to develop the necessary skills.
So where is the shortage? The real shortage lies in the experts who can oversee the entire battery value chain. While such individuals will become more prevalent as the industry matures, finding them is currently akin to searching for a unicorn.
That’s all for now. Until next time 🔋!
Thank you for reading this article. If you enjoyed it, feel free to share it with your friends.
You may also like:
It is not only North America and Europe. South Korea and Japan, countries with strong battery traditions, are also facing skilled worker shortages.
Here’s a nice report from EIT RawMaterials on the battery talent shortage: https://eitrawmaterials.eu/wp-content/uploads/2021/03/EIT-RawMaterials-Fraunhofer-Report-Battery-Expert-Needs-March-2021.pdf
Great insights! In your view, beyond waiting for the battery industry to mature, what would help cultivate more personnel who take a whole-of-value-chain view of batteries? Does it start at the level of public discourse? Policy framings? School curricula?