Lithium Horizons is a reader-supported publication. For deeper insights, including in-depth analysis, the latest developments, and expert insights into the energy and materials industries, subscribe below.
‘‘The 4680 is going to fail and never be successful.’’
― Robin Zeng, CATL Founder and Chairman
You've likely heard all the hype surrounding Tesla's 4680 battery cells. Introduced during Tesla's Battery Day in 2020, the 4680 cell format promises higher energy content and power capability. Four years later, this battery format has only been integrated into some Tesla vehicles produced at Gigafactory Texas, such as the Model Y and the Cybertruck.
The production of 4680 cells has encountered significant challenges. There have been rumors that Tesla has been recalling Cybertrucks equipped with these 4680 cells due to an issue termed "Cell Side Dent Induced Core Collapse." Additionally, CATL's founder, Robin Zeng, has publicly expressed skepticism about this battery format, stating outright that it will never work. Even Elon himself was on the verge of scrapping the project altogether. Nevertheless, it seems that Tesla has tapped China's Ningbo Ronbay New Energy and Suzhou Dongshan Precision Manufacturing to help reduce materials costs as it ramps up production of 4680 battery cells.
Tesla has been attempting to scale up the production of their 4680 cells for the past four years. According to their public announcements, in September 2024, they stated that they had produced their 100 millionth 4680 cell. Prior to that, in June 2024, they announced the production of their 50 millionth cell. This means that within a span of three months, they produced 50 million cells, equating to an annual production rate of 200 million cells. Given that each cell is estimated to have 87 Wh of energy, this translates to 17.4 GWh of 4680 cells produced per year.1 This is enough to quip 141 463 Cybertrucks with batteries.2
This is a promising achievement. But why is Tesla even considering the 4680 cells? Why go through all this trouble of introducing a new cell format?
Batteries come in three main geometrical formats: cylindrical, prismatic, and pouch. Cylindrical batteries are the most common format, and these are what you typically recognize as "the battery." They are packed into a cylindrical shape, which can vary in dimensions.
You may have heard of AAAA (also known as 08420), AAA (also known as 10440), or AA (also known as 14500) alkaline batteries or the larger 26650 battery, also known as the C format, or 62330, known as the D format. These are usually primary 1.5V alkaline batteries that use an alkaline (or basic; pH >7) electrolyte, such as potassium hydroxyde (KOH). They can also be found in lithium-ion variations, although the most common secondary lithium-ion batteries are those used for the automotive industry, like 18650, 21700, and 4680 (Figure 1).
These batteries are categorized according to their dimensions, specifically their diameter followed by their height. So, the 21700 label indicates a battery cell that is 21 mm in diameter and 70 mm in height (the last digit is there to indicate other potential modifications of the cell; Tesla has completely omitted this last digit in their naming convention for 4680 cells).
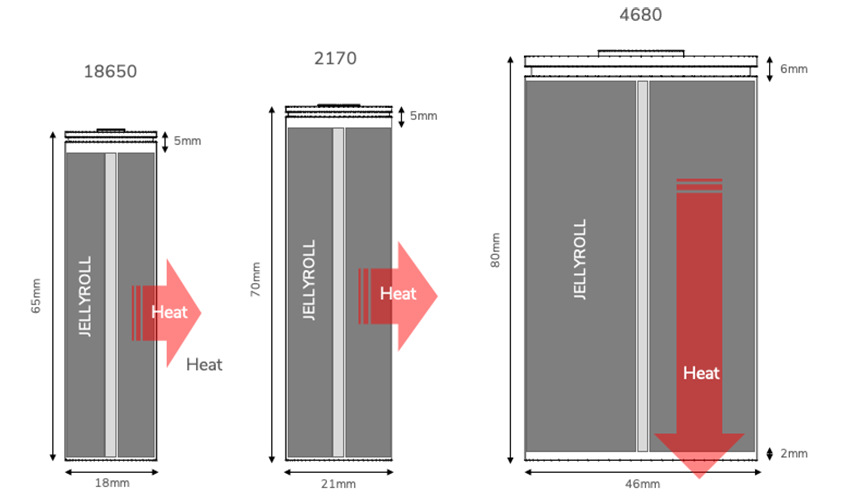
The 4680 cell format, with a 46 mm diameter and 80 mm axial length, promises higher energy content due to its larger size, which results in a higher ratio of "active" to "inactive" materials. Here, "active" refers to the materials within the cell directly involved in storing energy, while "inactive" materials are necessary components like the casing that don't directly contribute to energy storage. Larger cell formats have a higher ratio because the volume of active materials increases more than that of inactive materials as the cell size grows. The 4680 cell has more than five times the volume of the 21700 format.
Large-format cylindrical cells are also expected to reduce production costs in pack assembly because fewer individual cells are needed to be assembled and interconnected to achieve the same battery pack energy. This reduction in the number of components can streamline manufacturing processes, lower material costs, and decrease the complexity of wiring and connections within the battery pack.
Furthermore, the 4680 cell promises higher power due to its "tabless" design (Figure 2). Traditionally, lithium-ion batteries include tabs—small pieces of metal that connect the electrode (either anode or cathode) to the battery's positive and negative terminals. These tabs can create bottlenecks in current flow, increasing ohmic resistance and heat generation, which can affect the battery's efficiency and lifespan. In the tabless design, instead of having two tabs, the current collectors are patterned with multiple smaller connections or are designed so that the entire edge of the electrode can conduct current to the terminal, thereby improving the flow of electricity and heat. A considerable amount of heat is removed axially through the aluminum and copper current collectors to the bottom of the cell. This enables efficient bottom-side cooling of the battery pack and ensures more uniform temperature profiles within individual cells.
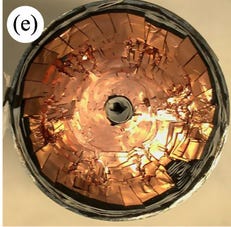
All of this is to say that Tesla is attempting to pack more energy into batteries at a lower cost. They recognize that they are at a significant disadvantage compared to companies like BYD, which are extremely vertically integrated, producing everything from batteries to electric vehicles in-house. Tesla cannot match this level of integration, however manufacturing their own batteries is critical, which will remain beneficial even as Tesla transitions into a robotics company. The question remains whether they can produce 4680 cells with low enough scrap yield, good cell-to-cell consistency, and low cost. Only time will tell.
That’s all for now. Until next time 🔋!
Thank you for reading. If you found the post interesting, consider sharing it with your network and subscribing. Such actions help spread the knowledge and support Lithium Horizons.
The 4680 cell from Tesla is estimated to have a specific energy of 244 Wh/kg with a weight of 0.355 kg per cell. This comes to roughly 87 Wh per cell.
A single Cybertruck has a battery pack of 123 kWh, so dividing 17.4 GWh with 123 kWh, you get 141 463.
The 4680 is not about higher energy density. It will have a lower energy density than other cells or cell formats. But this is mainly about costs. Also the dry coating is only about costs to safe on the expensive drying processes. By now, they probably have both electrodes done via dry processing.
Battery day promised a 5x increase in cell power. This fooled the mathematically challenged who could not figure out that the bigger cell has 5x the volume. It's another smoke and mirrors trick by Musk